Galvanic corrosion is a phenomenon that occurs when two dissimilar metals are in direct electrical contact and are also exposed to an electrolyte, such as water or saline solution. The pair’s more reactive (or less noble) metal becomes the anode and begins to corrode, while the more noble metal becomes the cathode and does not corrode.
When these two metals come into contact, an electrochemical reaction occurs, which causes electrons to migrate from the anode (the more reactive metal) to the cathode (the more noble metal). This flow of electrons results in accelerated corrosion of the anode while the cathode remains intact.
The galvanic series makes it possible to predict which metal will be the anode and which will be the cathode in a given pair of metals. The more significant the difference between the two metals in the galvanic series, the faster the galvanic corrosion will occur. For example, if zinc and stainless steel are in contact, the zinc will be the anode and corrode more quickly than the stainless steel, which will be the cathode.
Platinum |
Gold |
Silver |
Stainless Steel |
Copper |
Cast iron |
Steel |
Aluminum |
Zinc (galvanized steel) |
Magnesium |
THE GALVATECH SOLUTION, MORE THAN AN ALTERNATIVE
There are several ways to prevent galvanic corrosion:
1. Select metals with a minimum electrical potential difference. The table below indicates the acceptable combinations of metals and those to avoid to minimize the risk of galvanic corrosion depending on the choices of materials made.
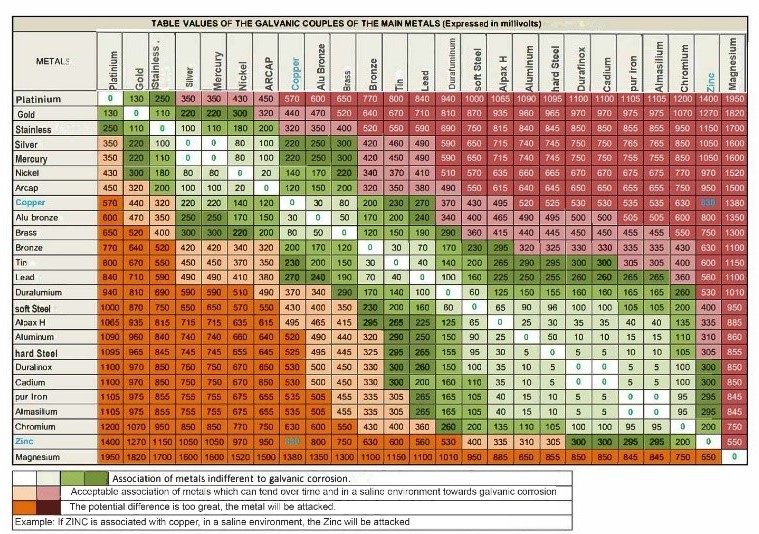
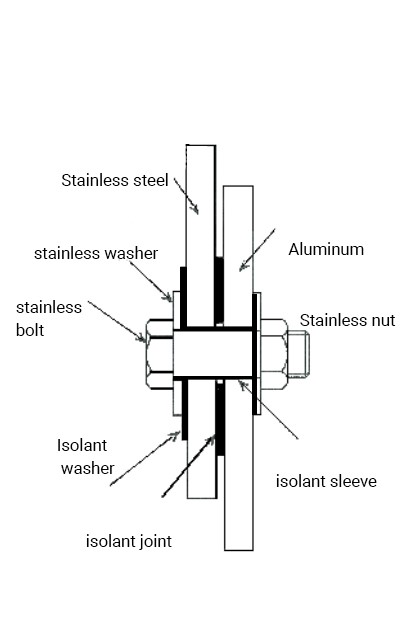
3. Use Rust-Anode coatings: Rust-Anode coating is an effective solution to protect steel structures against corrosion. Thanks to our zinc technology, our coatings offer galvanic protection by sacrificing themselves to preserve the steel, which will remain cathodic. By applying a layer of our product to the dissimilar metals in contact, our coatings will assume the anodic load of the assembly, thus preventing galvanic corrosion of the two metals in contact.
4. Use sacrificial anodes: by adding sacrificial anodes made of metal less noble than the other metals in contact, galvanic corrosion can be reduced by causing the sacrificial anode to corrode rather than the other metals. These anodes sacrifice their own durability to protect the nobler metal. For example, sacrificial zinc, aluminum, or magnesium anodes have been used to protect steel from corrosion in seawater.
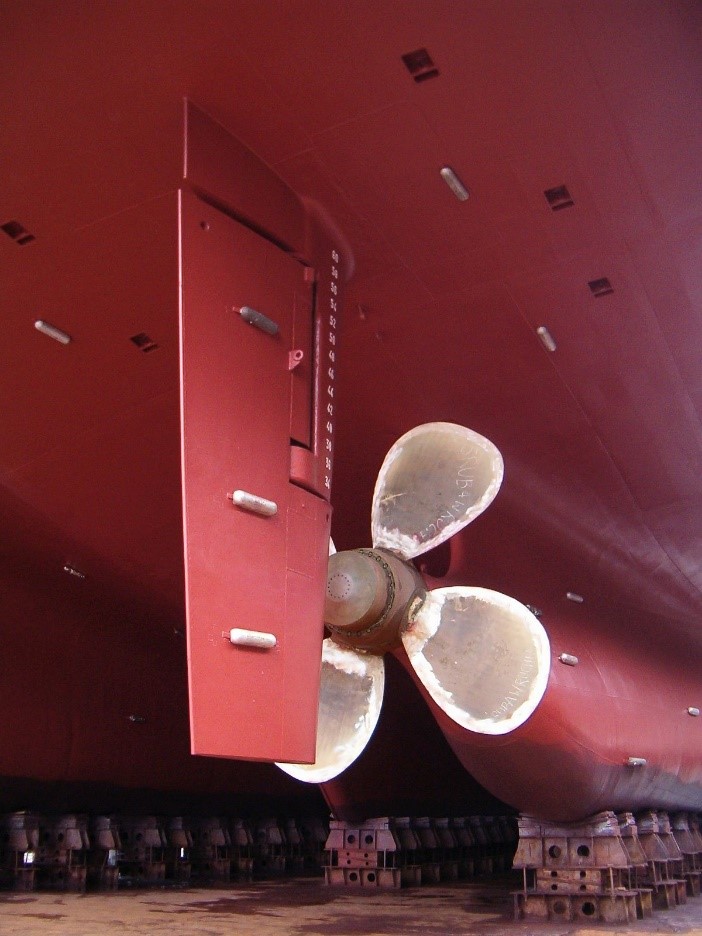
It is essential to underline that the prevention of galvanic corrosion starts from the project’s design, considering the choice of materials to avoid any contact between metals likely to cause this corrosion. Rust-Anode coatings are an effective solution for the protection of steel thanks to their cathodic protection mechanism, thus guaranteeing the durability of the treated structures.
Contact us to learn more. 1-888-743-2046