OVERVIEW
All humans on earth are now confronted that we are all on the same vessel. Mother nature is sending obvious signs and sometimes strong-arm messages like natural disasters of all kinds.
The energy productions of all types will have to be evaluated. Essential choices will have to be taken according to the environmental concerns and the human’s quality of life. The electric power industry is the backbone of America’s economic sectors, generating the energy that empowers its people and businesses in global commerce. Transportation, water, emergency services, telecommunications, and manufacturing represent only a few of the power grid’s critical downstream dependencies. Reliance on the electric grid is a crucial interdependency (and vulnerability) amongst all Critical Infrastructure and Key Resource (C.I.K.R.) sectors, plus supporting infrastructures, making grid reliability and resilience a fundamental need for national safety and security.
Today, the American and Canadian electricity sector is influenced by various new forces that can affect the future management and operation of the grid. Current drivers include the growing use of less expensive natural gas for power generation, the retirement of coal and fuel oil generation for carbon reduction, uncertainty in the long-term role of nuclear generation, rapid deployment of intermittent renewable energy technologies, severe weather, and growing jurisdictional interactions at government levels.
Industry experts predict that electric utilities will undergo more change in the next ten years than in the past hundred. Alternative energy, smart grids, and environmental concerns dominate industry headlines. While maintenance and asset health do not attract the public’s attention, a growing number of asset managers realize that new maintenance strategies can play a central role in making utilities nimbler, reliable, and, ultimately, more profitable.
The electric power industry is undergoing a period of rapid transformation. Issues such as the rapid adoption of renewable energy sources, a strong emphasis on resilience and the aging of the existing infrastructure are forcing system and grid operators to carefully consider how they expend their resources and optimize their operations.
Transmission towers and poles are among an electric utility’s largest and most important commercial assets. Unfortunately, as the need to generate profits and shareholder dividends has intensified, regular tower and pole maintenance investment has often been reduced or eliminated to cut costs. Ironically, such cost-saving measures can double or triple long-term maintenance costs while increasing the risk of power outages and public safety problems.
No matter where the future sources of energy are going to be, they will have to be transported. Therefore, proper maintenance evaluation and maximization of the tower structures will be critical factors. All structural assets will have to be potentially exploited, even mid-aged or old ones; meanwhile, some construction of harmonization or new adapted structures will occur. The ongoing energy transition toward decarbonization will require substantial investments.
For the last century, safe and reliable electricity has been the cornerstone of our modern society. While large portions of the general public may take this essential commodity for granted, utility professionals know just how much effort and resources go into keeping the lights on when it matters most.
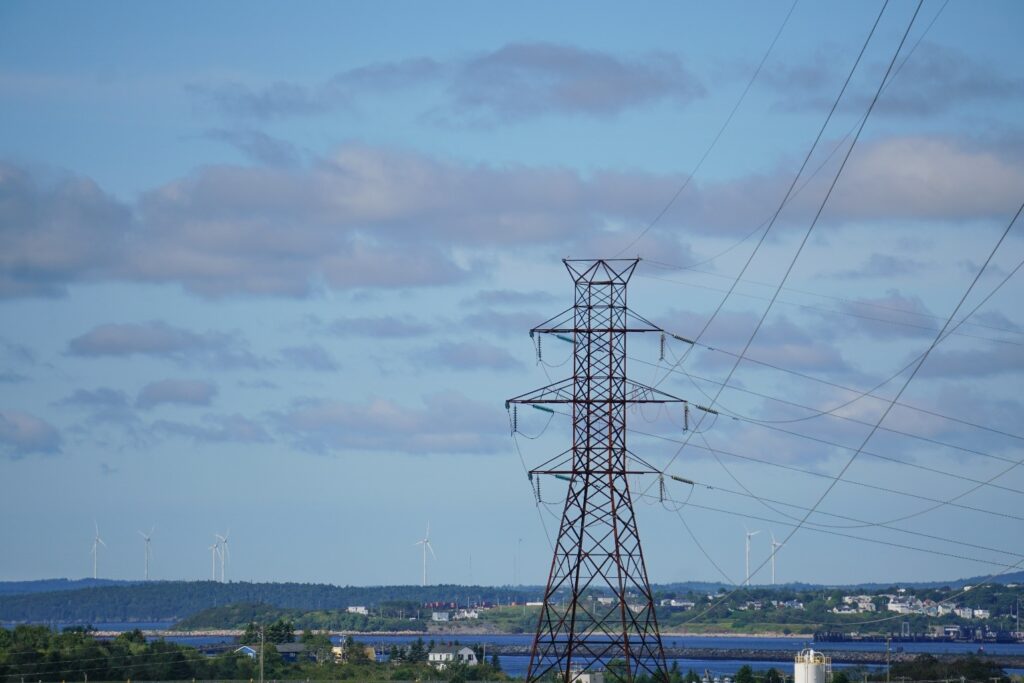
Long-term Cost Savings
In U.S.A, when electrical utilities were deregulated in the late 1980s, many immediately and dramatically dropped resources directed to transmission tower maintenance. Although utilities often owned or maintained thousands of transmission towers and poles, the goal shifted from delivering power to maximizing return on investment for many. Consequently, many of today’s transmission towers and poles need significant repair.
Utilities can save by actively maintaining large transmission towers and pole inventories to allow them to deteriorate before repair. In addition to saving millions of dollars, an active maintenance program delivers the benefits of increased employee and public safety, a lower risk for power outages, and the community’s goodwill for clean and attractive towers.
New vs. Existing Steel Structures
The argument against implementing aggressive maintenance programs for electric utility transmission and distribution steel structures may have been based on the belief (now known to be misguided) that steel lasts forever. Under that assumption, more of a utility company’s capital expenditure dollars would be allocated for building more steel structures to keep up with the development of intelligent grids rather than developing more aggressive maintenance programs to extend the service life of its existing systems. As a result, more utility money is available to build new structures, so maintenance often receives less funding.
That belief that steel has unlimited longevity is no longer valid, of course, as utility companies have watched their aging steel transmission towers and distribution structures succumb to the ravages of corrosion. Steel corrodes and requires regular inspection and maintenance, but it’s often a budget issue that prevents utility companies from implementing a detailed maintenance program. For example, some maintenance projects can be very costly, such as where lead abatement and recoating are performed on a structure to comply with federal, state, and local regulations regarding tower visibility requirements for air traffic. Maintenance money is sometimes hard to obtain and secure for special projects like steel structure maintenance.
As the building of the North American smart grid continues to gain momentum, however, it’s reasonable to expect that more dollars will be made available to build new structures to accommodate the restructuring of the electric power grid. And in many cases, money to replace old systems is more readily available. However, some believe the tide may be turning, and more electric utility companies will start developing maintenance programs to repair and preserve their current inventory of steel transmission and distribution structures as it becomes more cost-effective. In addition, the proper inspection and maintenance programs can pay dividends by extending structure life and increasing system reliability. Geographically, North America has a very diverse climate, which influences the type of inspections needed. In addition, many maintenance projects are now underway in the Southeast and along the East Coast due to the climate and other environmental conditions being more corrosive.
Now, some utility companies are waking up to the need for maintenance programs because state public utility commissions and the Department of Homeland Security are urging them to improve their maintenance programs.
Some state utility commissions are balking at rate increase requests from electric utilities, forcing the utility companies to consider maintenance programs a higher priority.
Exponential Corrosion Principle
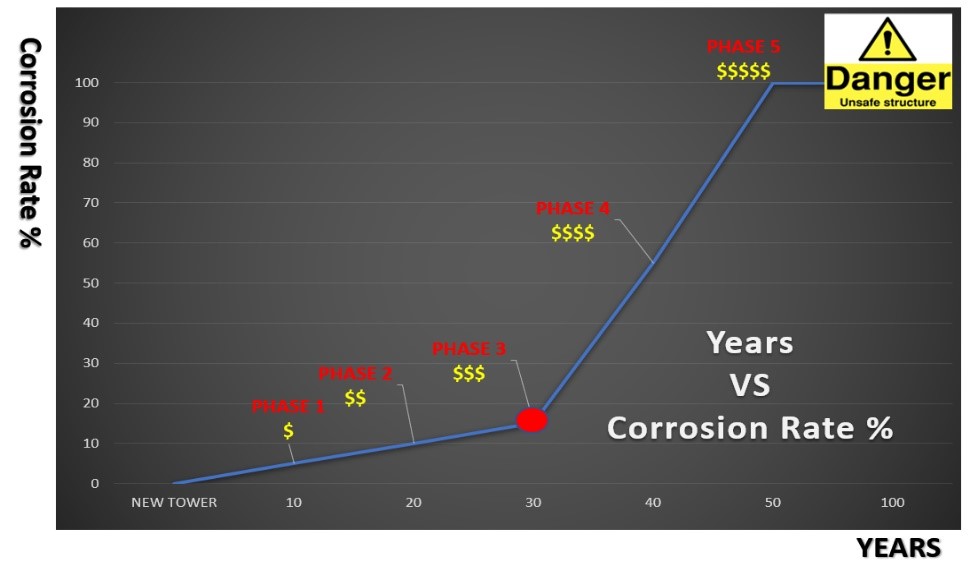
More than 3,000 electric utilities operate hundreds of thousands of transmission towers in the U.S. These poles and latticework of galvanized steel typically range from 50 to 180 feet in height but can reach 900 feet or more. In the U.S., most of these structures were built between 1960 and 1990, which means they have had or will soon need maintenance and repairs.
Depending on where they are located, in harsh and mild environments, galvanized transmission towers and poles can function for 15 to 50 years before showing the first signs of corrosion. Meanwhile galvanized steel in rural or desert settings may remain rust-free for up to 80 years.
Once a galvanized transmission tower or pole corrode, the corrosion advances exponentially. A tower structure or a pole with less than 5 percent rust at age 30 can oxidize to the point of failure within 10 years. More critically, as the tower or pole corrosion accelerates, the repair time and labour and materials cost may increase.
Corrosion damage is one of the more pervasive threats to the structural integrity of steel poles, lattice towers, and other utility transmission assets. For a material type that was once considered relatively maintenance-free compared to wood structures, the industry now realizes that steel structures do, in fact, require proactive inspection and remediation.
With limited budgets and rising pressure from customers and regulators to meet sustainability and reliability goals, these businesses face tough decisions about which infrastructure upgrade projects to support. When problems are identified, stakeholders must decide whether to make minor, lower-cost repairs to increase the time from failing assets or make significant investments in upgrades that require far more time and capital but will last longer and support future expansion goals. There is always pressure to make short-term, small-cap decisions. But it often creates the weakest link, which becomes one of the most severe threats to asset owners. Convincing executives and regulators to make proactive investments in infrastructure can be challenging. But when companies fail to take such an approach, they increase the likelihood of facing emergencies and the resultant high costs of repairing failed infrastructure. As a result, the cost of responding to a crisis is so much higher than a planned response. Therefore, you pay a premium price for all activities in crisis response. Companies also risk a negative impact on their brands, affecting current and future business. So, the cost-benefit makes better business sense to spend more money on upgrades that will deliver a higher level of integrity for the long term.
However, cost should not be the only factor considered, says Curt Pohl, vice president of distribution for NorthWestern Energy, a power utility in Butte, Montana, that serves Montana, South Dakota and Nebraska. “You have to balance cost against risk to reliability and performance,” he says. Striking the right balance requires practical project management tools and processes to complete thorough due diligence and risk assessment. He says the project team has the necessary resources and leadership in delivering. “A strong project management framework gives you the confidence to execute your plan successfully.”
Risk and efficiency drive investment
The infrastructure problem: short-term fixes or long-term strategy?
Perhaps that is why operational failure ranked first among concerns related to ageing infrastructure. Many executives in these industries cited risk to operations as a top decision-making factor.
Managing and Budgeting for Repairs
When corrosion begins to consume a transmission tower or pole, the key to managing repair costs is to arrest its progress before the unit transitions from one phase of corrosion to the next. For electric utilities, the optimal solution is to repair the entire inventory of towers and poles as early as possible in Phase I, when it is less costly. Unfortunately, that is impossible for most utility companies because of budget constraints and the varied ages of the towers and poles in their inventory.
Infrastructure availability, sustainability, return on investment (R.O.I.) and economics
Extending assets life by replacing equipment such as towers is expensive. Electric utility owners may be especially reluctant to spend money on replacing assets in an era of rapid transformation. Extending asset life through proactive maintenance strategies can give electric utilities more time to consider options.
Proactive vs corrective maintenance
Proactive maintenance strategies use corrective, preventive, and predictive processes to complement one another. Industry studies indicate that the average utility spends more than 55% of its maintenance budget on reactive maintenance, the highest cost. In comparison, the top-tier companies that utilize predictive technologies and proactive practices spend less than 10% of their budget on reactive strategies. Today, leading utilities continue to expand the adoption of Condition-Based Maintenance (C.B.M.) processes based on real-time and historical data collection and analytics to reduce the high cost of reactive maintenance strategies.
IMPORTANT CONSIDERATIONS TO SECURE STRUCTURES STEEL INTEGRITY AND YOUR INVESTMENTS
Coatings Acting as Barrier Protection (Non-Active) :
For decades, this traditional type of coating (mostly alkyds) has provided no active protection against corrosion once dry. Instead, it works as a shield for the remaining galvanized or rust surfaces. This form of protection lacks interaction with the existing substrate, serving only to prevent moisture and contaminants from increasing corrosion levels for a short or medium period, depending on the initial condition of the towers and their environmental exposure. While less costly initially, it’s important to note that corrosion may develop beneath the applied barrier layer when the coating weakens, concealing defects that could potentially harm the structures’ integrity.
Coatings with Active Cathodic Protection :
Primarily zinc-based and suitable for hot-dip galvanized and rust layers, these coatings offer galvanic protection in addition to preserving the existing galvanized zinc layer. Once dry, these coatings, being anodic to the steel or complementary to hot-dip galvanized, actively protect against corrosion. This approach proves to be less costly over time, providing a comprehensive solution for long-term structural integrity.
Galvatech’s Revolutionary Galvanizing Compound Rust-Anode :
Galvatech’s groundbreaking Galvanizing Compound Rust-Anode represents an innovative solution at the forefront of preserving and enhancing the structural integrity of aging transmission towers. In an era where the electric power industry is undergoing rapid transformation, Galvatech and its Galvanizing Compound stand as leaders in proactive maintenance, countering corrosive forces that threaten the reliability of steel structures. Meticulously designed to actively protect against corrosion, this advanced technology acts as an active cathodic protection, such as the hot dip galvanized process that significantly extends the life of transmission towers for decades. With the Galvanizing Compound, utilities now have a cost-effective and efficient tool to fight corrosion, ensuring long-term savings, increased safety, and sustained public goodwill.
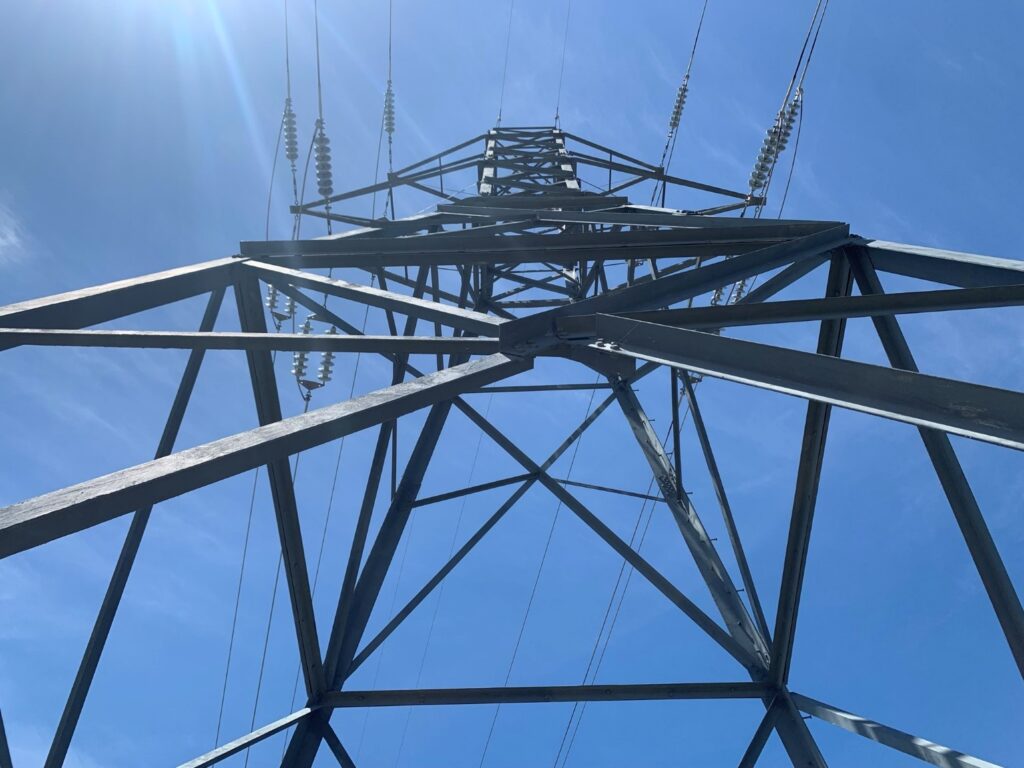
Conclusion
In conclusion, the comprehensive exploration of maintenance strategies in the electric power industry underscores the substantial advantages of preventive maintenance, as highlighted throughout the article. The implementation of proactive measures, such as Galvatech’s Galvanizing Compound Rust-Anode Primer, not only presents a cost-effective solution but also contributes to significant benefits. By embracing preventive maintenance, utilities can achieve reduced capital costs through the extension of asset lifecycles, leading to lower maintenance expenses over time. The emphasis on better asset reliability, improved asset availability, and enhanced asset utilization further solidifies the importance of a proactive approach. Notably, preventive maintenance allows for longer asset lifecycles and more informed capital expenditures, optimizing the overall maintenance interval. The proactive identification and addressing of potential issues minimize lost production time by accurately predicting failures. In essence, this global approach not only safeguards the structural integrity of transmission towers but also establishes a foundation for a resilient, cost-efficient, and reliable electric power industry.
Claude Dupont
Gavatech2000
Director – North America
Research and Development
Corrosion Specialist, Zinc strategies & Solutions, All New & Corroded Metals
claudedupont@galvatech2000.com
galvatech2000.com
External Sources
- MATERIEL PERFORMANCE – NEW STANDARDS PROVIDE MAINTENANCE GUIDELINES FOR THE ELECTRIC POWER INDUSTRY – BY TRUDY SCHREINER – MAY 2020
- JPCL – CORROSION MANAGEMENT OF ELEVATED LATTICE GALVANIZED – MARK B. DROMGOOL – KTA – AUSTRALIA – AUG 2016
- TRANSMISSION PLANNING WHITE PAPER – RALPH LUCIANI & MAGGIE SHOBER NAVIGANT CONSULTING – JAN 2014
- TAUBE B, LEUFKENS P, WEIK J, DILL J. WHITE PAPER: PROACTIVE TRANSMISSION AND DISTRIBUTION ASSET MANAGEMENT UTILIZING ADVANCED DATA MANAGEMENT AND PREDICTIVE ANALYTICS. 2016 OCT 28
- ELECTRICITY TRANSMISSION – A PRIMER – NATIONAL COUNCIL ON ELECTRICITY JUNE 2004
- THE ECONOMIST INTELLIGENCE UNIT – THE IMPACT OF AGEING INFRASTRUCTURE IN PROCESS MANUFACTURING INDUSTRIES – APRIL 2014
- T&D WORLD – MANAGING THE POWER GRID’S VULNERABILITIES – BY GENE WOLF DEC 2021
- NACE SP0215-2015/IEEE STD 1839-SG, NACE INTERNATIONAL AND IEEE JOINT STANDARD PRACTICE FOR BELOW-GRADE CORROSION CONTROL OF TRANSMISSION, DISTRIBUTION, AND SUBSTATION STRUCTURES BY COATING REPAIR SYSTEMS
- NACE SP0315-2015/IEEE STD 1835-SG, “STANDARD FOR ATMOSPHERIC (ABOVE GRADE) CORROSION CONTROL OF EXISTING ELECTRIC TRANSMISSION, DISTRIBUTION, AND SUBSTATION STRUCTURES BY COATING SYSTEMS”
- NACE SP0415-2015/IEEE STD 1895-SG, NACE INTERNATIONAL AND IEEE JOINT STANDARD PRACTICE FOR BELOW-GRADE INSPECTION AND ASSESSMENT OF CORROSION ON STEEL TRANSMISSION, DISTRIBUTION, AND SUBSTATION STRUCTURES
- EE ONLINE – TRANSMISSION LINE OPERATIONS AND MAINTENANCE – BY FINN RIMMER – MARCH 2005
- EXO ENGINEERING – CUSTOMIZING A LATTICE TOWER STRUCTURAL HEALTH & CORROSION ASSESSMENT PROGRAM
- (U.S. DEPARTMENT OF ENERGY OFFICE OF ELECTRICITY DELIVERY AND ENERGY RELIABILITY)
- NACE INTERNATIONAL IMPACT – INTERNATIONAL MEASURES OF PREVENTION, APPLICATION,AND ECONOMICS OF CORROSION TECHNOLOGIES STUDY – MARCH 2016
- AMPP – INTRODUCTION TO STRUCTURAL STEEL PRIMER SELECTION